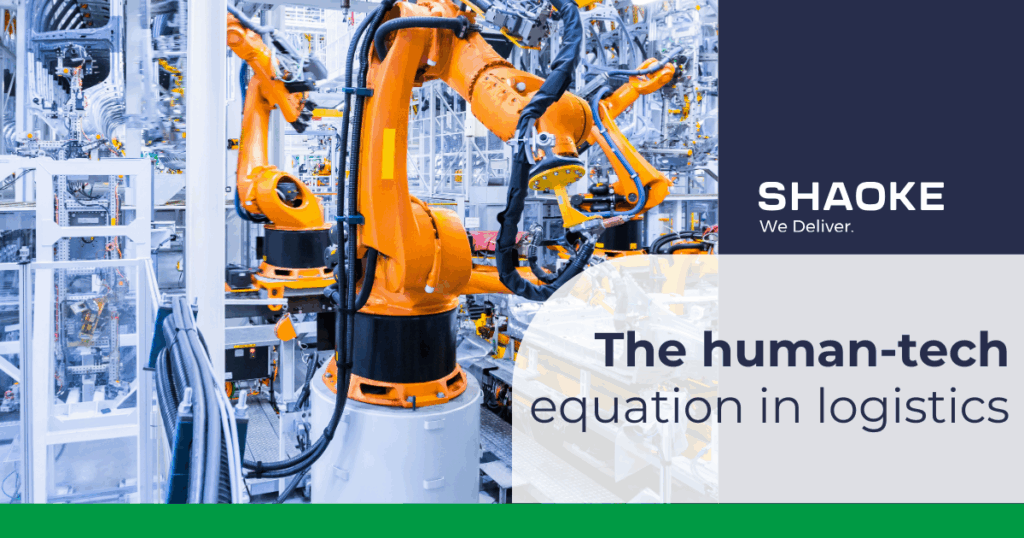
The shift toward warehouse automation is accelerating. According to McKinsey, the global warehouse automation market is expected to grow from $15 billion in 2019 to over $30 billion by 2026. In e-commerce, where speed and accuracy are critical, technologies like autonomous mobile robots (AMRs), automated storage and retrieval systems (AS/RS), and AI-driven warehouse management systems (WMS) are increasingly common. Retailers like Amazon and JD.com lead this trend, having deployed tens of thousands of robots to streamline fulfillment. But with all this tech, where does the human workforce stand?
Despite the hype, full automation isn’t always the goal – or even realistic. A study from the World Economic Forum (2023) shows that 64% of logistics companies use a hybrid model, blending machines with human labor. While robots excel at repetitive tasks, they struggle with handling irregular items, adapting to unexpected situations, or communicating with teams. DHL, for example, still employs over 570,000 people worldwide and recently stated that automation is there to “support, not replace.” For smaller firms, the cost and complexity of full automation remains a significant barrier.
Labor shortages in logistics continue to affect operations. The International Road Transport Union reported that over 2.6 million truck driver positions went unfilled globally in 2023. In warehousing, the U.S. Bureau of Labor Statistics noted that job openings in the sector remain consistently above pre-pandemic levels. Automation can ease some of the strain, but attracting and retaining skilled logistics workers remains essential – particularly in peak seasons when human adaptability matters most.
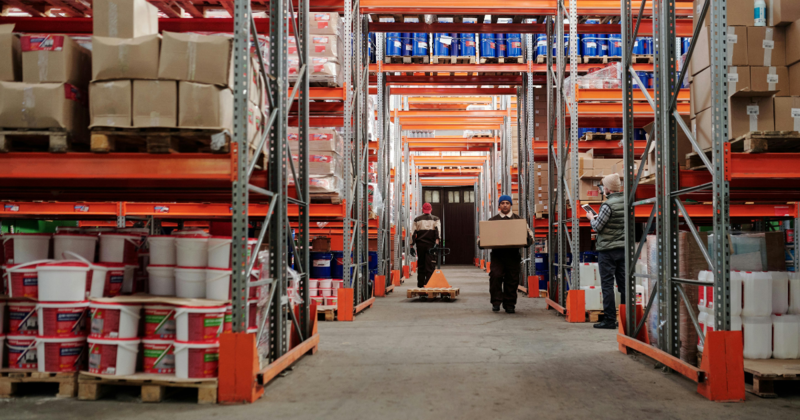
Worker satisfaction and safety are also key considerations. Research from MIT’s Work of the Future project indicates that mixed human-robot environments reduce worker fatigue and injury risk by taking over the heaviest tasks. But the same report warns that poor implementation can lead to job dissatisfaction, especially when workers feel monitored or easily replaceable. Effective integration of automation involves training, clear communication, and including workers in system design.
For logistics companies, especially those dealing with the rapid import volumes driven by platforms like Shein, Temu, and DHgate, flexibility is everything. These discount giants ship millions of small parcels that require fast sorting, customs clearance, and last-mile delivery. Automation helps with speed, but it’s the local workforce that manages exceptions, negotiates with customs, and handles customer concerns – tasks where tech still lags behind.
In the end, the winning formula combines automation with human skill. It’s not a question of machine or person – it’s about how the two can work better together. Logistics leaders must invest in both: smart systems and skilled teams. Because even the best robot won’t resolve a customs delay with a phone call, nor will it calm a stressed-out warehouse crew during peak season. Real logistics needs real people – with a bit of robotic help.
Sources:
- McKinsey & Company (2021): “Automation in logistics: Past, present, and future”
- World Economic Forum (2023): “The Future of Jobs Report”
- International Road Transport Union (2023)
- U.S. Bureau of Labor Statistics (2024): Warehouse Job Openings and Labor Turnover
- MIT Work of the Future (2022)
- DHL Group Reports and Sustainability Updates